Design of Plastic Medical Tray: A Case Study of Orthopaedic Implant Packaging
Keywords:
Plastic medical tray, Medical device, Packaging design, Packaging analysisAbstract
The plastic medical tray is commonly used for medical device packaging such as the implant or surgical instruments. The tray can be undergone gamma-ray exposure to sterilizing the medical devices inside. The tray keeps medical devices free from micro-living organisms and protects them from contaminated external environments. The plastic sheet is usually used for producing the tray which turns into a final tray shape using thermoforming. During the tray design process, factors such as the dimension of medical devices, ergonomics, and strength, have to be taken into consideration. Computer-Aided Design/Three-dimensional Printing (CAD/3DP) technologies were applied for verification of the tray geometry whereas finite element methods are applied for strength analysis. Three-dimensional (3D) models of the tray, which are referenced from the dimension of medical device, were 3D printed to test ergonomics for operating room (OR) nurses handling. After that, 3D models were evaluated the strength to ensure safety during delivery. From the analysis, the geometry of the tray was appropriate for handling with sufficient strength. The bottom corner of the tray is a critical point since it presents a high-stress magnitude. The load of 54.6 kg-f deforms the tray was less than 0.5-
mm, confirming the vertical stack storage.
References
American Society for Testing and Materials.(2014). Standard test method for tensile properties of plastics (ASTM D638-14).
Retrieved from https://www.astm.org/Standards/D638
Bix, L., & Fuente, J. (2009). Medical device packaging. In K. L. Yam (Ed.), The Wiley encyclopedia of packaging technology. Hoboken, NJ: John Wiley & Sons.
Hindelang, F., Zurbach, R., & Roggo, Y. (2015). Micro Computer Tomography for medical device and pharmaceutical packaging
analysis. Journal of Pharmaceutical and Biomedical Analysis, 108, 38-48. doi:10.1016/j.jpba.2015.01.045
Kinsel, D. (2012). Design control requirements for medical device development. World Journal for Pediatric and Congenital Heart Surgery,
(1), 77-81. doi:10.1177/2150135111422720
Reymondon, F., Pellet, B., & Marcon, E. (2006). Methodology for designing medical devices packages based on sterilisation costs. IFAC
Proceedings Volumes, 39(3), 701-706.doi:10.3182/20060517-3-FR-2903.00355
Silindir, M., & Özer, A. Y. (2009). Sterilization methods and the comparison of e-beam sterilization with gamma radiation sterilization. FABAD Journal of Pharmaceutical Sciences, 34, 43-53.
Tarathikhun, P., Chantarapanich, N., Valeeprakhon, T., & Wanchat, S. (2018). Mechanical properties of fused deposition modeling parts. International Scientific Journal of Engineering and Technology, 2(2),38-44.
Wasikiewicz, J. M., Roohpour, N., Paul, D., Grahn, M., Ateh, D., Rehman, I., & Vadgama, P. (2008). Polymeric barrier membranes for
device packaging, diffusive control and biocompatibility. Applied Surface Science, 255(2), 340-343. doi:10.1016/j.apsusc.2008.06.159
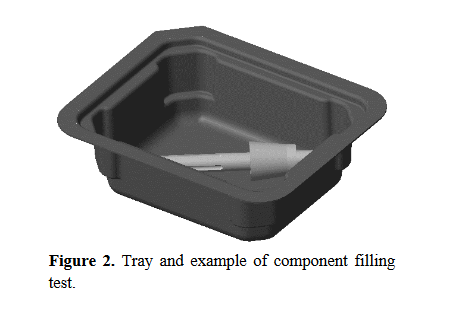